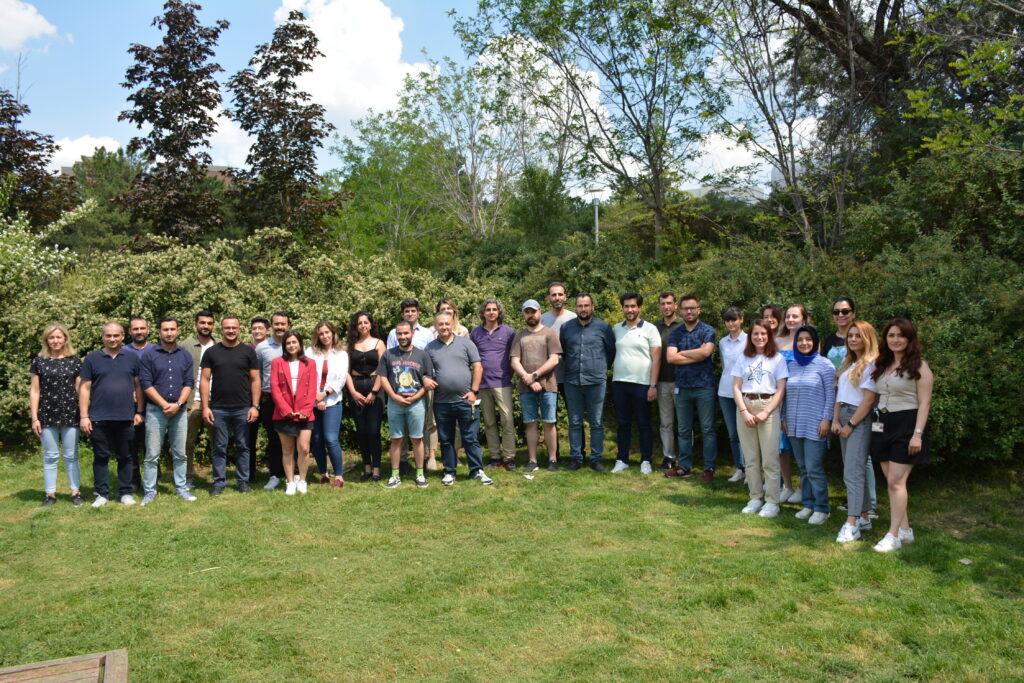
GÜNAM Photovoltaic Pilot Production Line (GPVL)


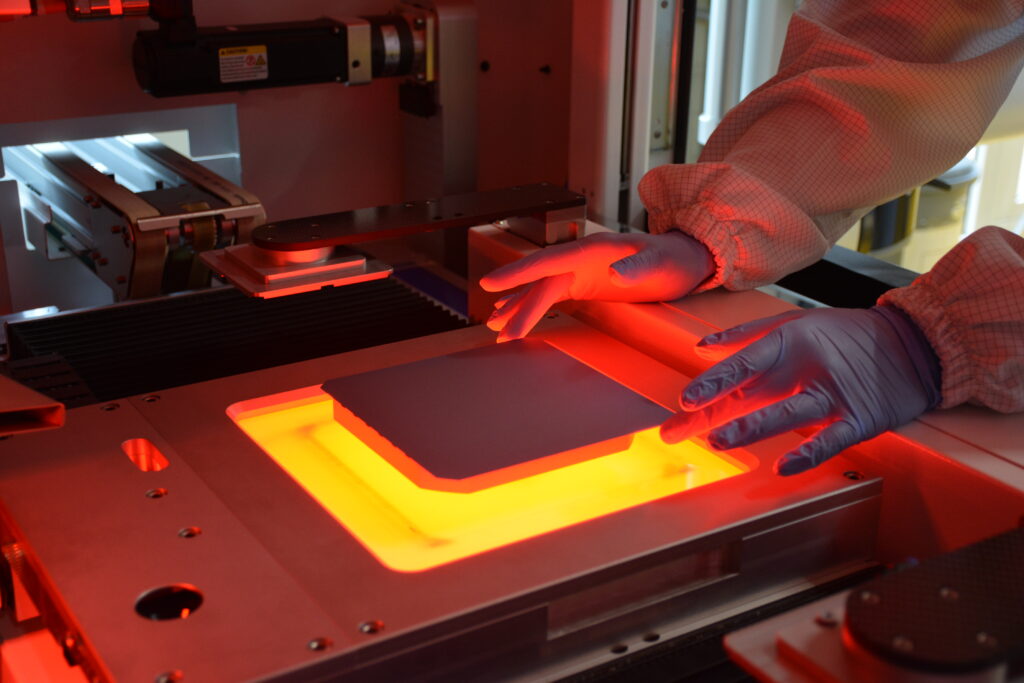



ODTÜ-GÜNAM’s GPVL facility which approximately has 600 m2 production area with 100 wafers/h manufacturing capacity is mainly capable of producing PERC/PERT/PERL/IBC type industrial size silicon solar cells. GPVL infrastructure with >20 researchers is serving as a fully integrated pilot production area from Si wafers to solar cells.
The cell line is mainly equipped with:
- Fully automated wet benches for mono wafer texturing and junction isolation;
- Industrial diffusion furnaces for p and n-type doping;
- Spatial Atomic Layer Deposition (ALD) tool for Alumina (Al2O3) coating to passivate of p-type silicon wafers;
- PECVD for dielectric (i.e. SixNy, SiOxNy) deposition and LPCVD for a-Si deposition;
- Picosecond laser for contact opening and scribing/cutting
- Fully automated screen printing and firing equipment
- Ion implanter for p and n-type doping of industrial scale c-Si wafers
- Multi-source PVD system for metal evaporation;
- Plating systems for plated contacts (Ni/Cu/Ag);
GPVL building and infrastructure are supported by the Ministry of Development (Turkey), and the PERC cell production equipment is funded in the scope of the MİLGES Project (development and installation of the first national PV power station of Turkey from solar cell to power station components) supported by TÜBİTAK (The Scientific and Technological Research Council of Turkey).
Cleanroom
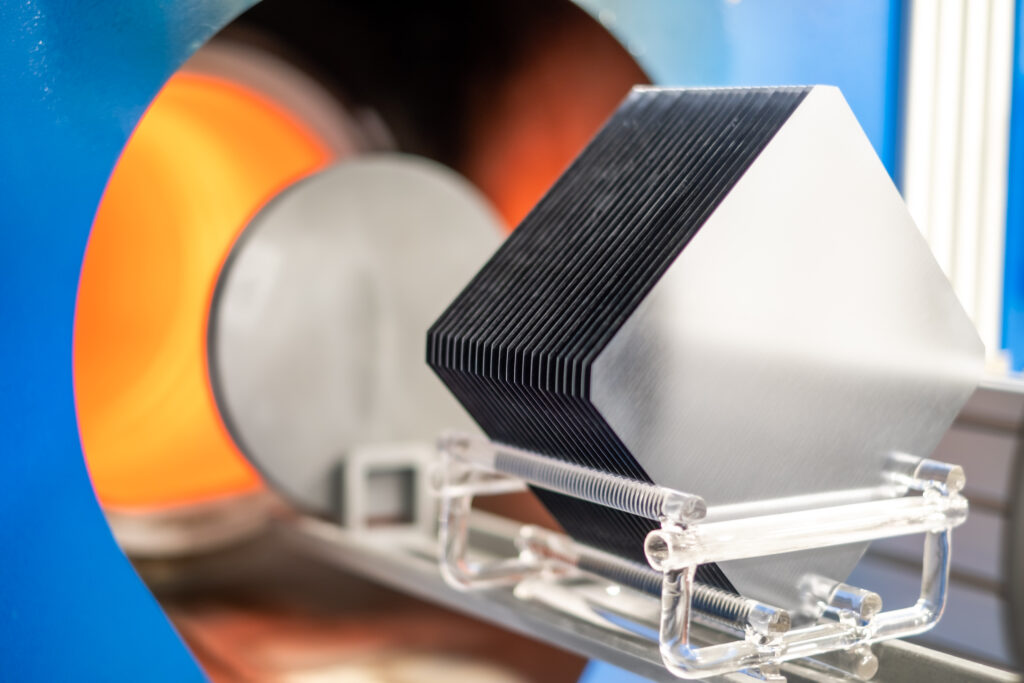
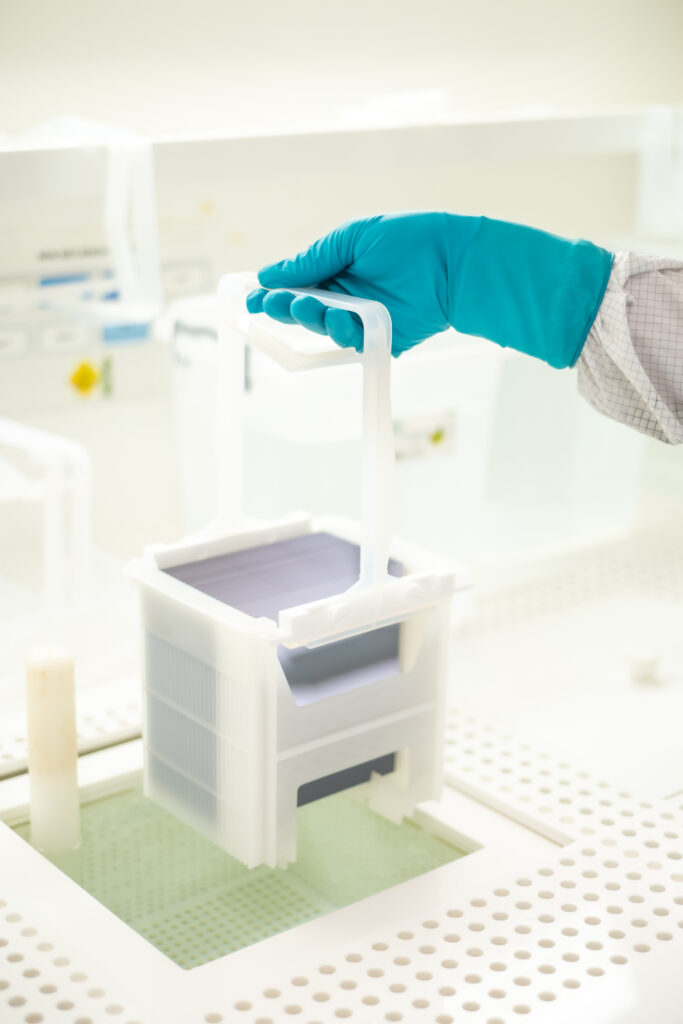

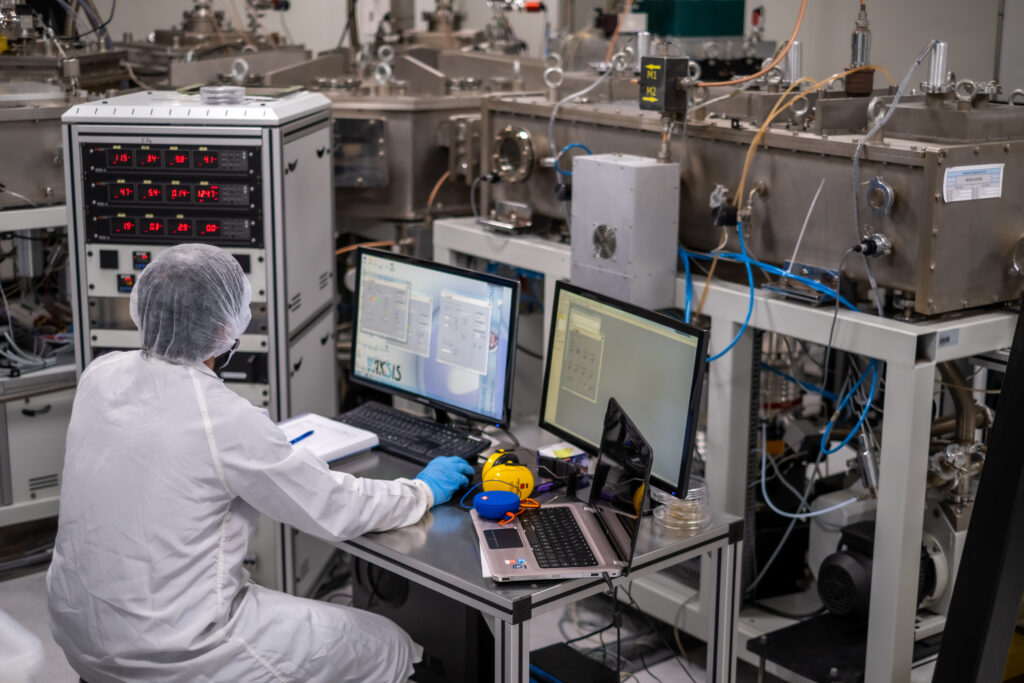
ODTÜ-GÜNAM’s cleanroom facility consists of four divisions with a total lab area of 150 m2. Crystalline Si and Si-based thin-film production tools are located in the main hall of the facility. There are separate rooms for wet chemical processing and photolithography.
In the lithography room, there exists one mask aligner, one spin coater, and one drying furnace to make the whole photolithography process. In the chemical room, all wet chemical processes from the unpacked Si wafer till the final device could be done. Surface texturing, saw damage removal, PSG and BSG removal after diffusions, and standard (RCA-1, RCA-2, etc.) cleanings are the most frequent processes. There are 3 wet benches and 1 nitrogen dryer placed in the chemical room.
There is also a separate test and characterization room equipped with Sinton Lifetime Tester, Flash & Continuous Solar simulators, Raman, Spectroscopic Ellipsometer, Photoluminescence Imaging, Profilometer and Four Point Probe tools.
The cleanroom is mainly equipped with:
- Wet benches for mono wafer texturing and cleaning purposes
- High-temperature diffusion (POCl3 and BCl3) furnaces for p and n-type doping
- Oxidation furnace
- PECVD system for SiNx deposition
- Photolithography process equipment with a mask aligner, spin coater, drying oven
- A cluster tool for heterojunction and thin-film Si solar cell production
- Reactive ion etching (RIE) system
- A Single side etching system
- Oxygen plasma system
- E-beam evaporation system for Silicon
- A nanosecond laser thin film scribing.
Metallization Laboratory
Metallization is the last step of the solar cell fabrication sequence. While screen printing can be used as an industrial method, for smaller sample sizes and different requirements; thermal, physical or electron beam evaporation methods could also be used. Although all these mentioned systems are available in ODTU-GUNAM laboratories, screen printing is the most applied method. During screen printing, the metal paste is screen printed using a screen which is then dried and finally exposed to high temperature firing for activation. The metallization laboratory is mainly equipped with:
- Screen printer
- Firing furnace
- Drying furnace
- Thermal evaporation system
- Physical evaporation system
- E-beam evaporation system
Metal Paste Laboratory
ODTÜ-GÜNAM also develops silver-based pastes and gum for crystal silicon and shingle cells. Synthesis reaction in its infrastructure, the contribution of different silver structures to the paste is examined. In addition, different glass frit compositions are considered with a high temperature furnace and bilyalı değirmen. Pastes are formed in a rotary evaporator and concentrated with 3 roll mill. Paste rheology is considered with a thermomechanical analysis setup.